Abstract
Este manuscrito describe la fabricación de microagujas polimérico (MN) matrices mediante fotolitografía. Se trata de un proceso libre de moho sencilla utilizando una fotomáscara que consta de microlentes incrustadas. No se encontraron microlentes incrustadas para influir en la geometría MN (nitidez). MN matrices sólidas con diámetros de punta que oscilan entre 41,5 micras ± 8,4 micras y 71,6 micras ± 13,7 m, con dos longitudes diferentes (1336 m ± 193 micras y 957 micras ± 171 micras) se fabricó. Estas matrices MN pueden proporcionar aplicaciones potenciales en el suministro de agentes terapéuticos de bajo peso molecular y macromolecular través de la piel.
Introduction
Administración transdérmica de fármacos ofrece un enfoque alternativo atractivo para la administración de fármacos, especialmente para las biomoléculas, que se administran casi exclusivamente por inyecciones hipodérmicas. Sin embargo, la piel, especialmente la capa superior (el estrato córneo), es una barrera formidable prevención de moléculas exógenas de entrar en el cuerpo humano. Recientemente, los dispositivos MN se han convertido en herramientas que permite entregar medicamentos a través de la piel. Los dispositivos MN crean poros temporales dentro de la capa córnea para permitir el paso de moléculas de fármaco para conseguir la actividad fisiológica deseada con un mejor cumplimiento y conveniencia 1 a 3 paciente.
Varios métodos de fabricación se han adoptado para fabricar los MNs poliméricos 4. Sin embargo, por lo general implican procesos de pasos complicados y múltiples que requieren tiempos largos y / o altas temperaturas para fabricar matrices Mns. 4 Para simplificar el proceso de fabricación, un solo proceso libre de moho paso utilizandouna fotomáscara fue desarrollado recientemente 5,6. Sin embargo, con este método, inventado los MNs tenían puntas de las agujas romas, como ningún mecanismo estaba en su lugar de modificar la trayectoria ultravioleta (UV) que participan en la fotolitografía.
En este estudio, se han propuesto microlentes incrustadas en la fotomáscara para definir la geometría de los MNs. El protocolo para fabricar máscaras que constan de microlentes incrustadas y posteriormente MN fabricación con puntas afiladas utilizando el fotomáscara se reportan.
Subscription Required. Please recommend JoVE to your librarian.
Protocol
1. fotomáscara Fabrication
- Limpiar una oblea de 4 "de vidrio con solución Piranha (H 2 SO 4 / H 2 O 2 en 2: 1 ratio) durante 20 min a 120 ° C por inmersión en un tanque de cuarzo.
- Depositar una capa de cromo / oro (30 nm de Cr / 1 m de Au) capa sobre la oblea de vidrio usando un haz de electrones evaporador 7 (Figura 1A).
- Coloque las obleas en un evaporador de haz de electrones. Una vez que el vacío alcanza 5 x 10 -6 Torr, encienda la fuente de alta tensión (10 kV). Controlar el espesor del panel de control del monitor.
- Pre-limpia cada material durante 30 segundos usando la pistola de haz de electrones, manteniendo el obturador "OFF" (con el fin de evitar la deposición sobre las obleas).
- Generar una capa de máscara fotoprotector Cr / Au de profunda grabado húmedo del vidrio.
- Aplicar un fotorresistente gruesa 2 micras por hilado 5 ml de la solución durante 30 segundos a 3.000 rpm usando un sistema recubridor de spin-pulverización.Precocción la fotoprotección en una placa caliente a 100 ° C durante 1,5 min.
- Exponer y hornear dura la fotoprotección a 120 ° C durante 30 minutos en un plato caliente. Es crítico para generar una superficie hidrófoba y una fuerte adherencia de la resina fotosensible a la capa de metal. Patrón de la capa de Cr / Au usando Cr y Au reactivos de ataque a través de la máscara fotorresistente 8,9.
- Para la protección de la superficie de vidrio no-modelado, unir temporalmente la oblea de vidrio a una oblea de silicio maniquí. 9
- Coloque la oblea de vidrio sobre una placa caliente a 110 ° C y derretir la cera en el lado opuesto de la oblea de vidrio (de tal manera que toda la superficie de la oblea se cubre con cera).
- Coloque una oblea de silicio maniquí en contacto con la oblea de vidrio y presione para eliminar el exceso de cera. Con el fin de evitar el derramamiento de la cera, coloque un pañuelo de papel limpia habitación en la zona de cocción.
- Realizar ataque isotrópico de la lente utilizando ácido fluorhídrico optimizado (49% v / v)y ácido clorhídrico (37% v / v) solución (en una relación volumétrica de 10: 1). con un agitador magnético durante 8,5 min 10 Presencia del HCl es crítico en la consecución de una buena calidad de la superficie de las lentes generados.
- Asegúrese de que la velocidad de ataque es de 7 m / min; utilizando un volumen total de 200 ml de solución de ataque. Realizar el grabado en un recipiente de plástico y tomar las precauciones de seguridad para esta etapa de procesamiento.
- Limpie la oblea en el (DI) agua desionizada por lavado y posterior secado a temperatura ambiente.
- Después de la terminación del proceso, separar la oblea de vidrio a partir de la oblea de silicio maniquí y calentar la cera usando una placa caliente a 100 ° C durante 15 seg. A medida que la cera se funde a esta temperatura, separar la oblea de vidrio a partir de la oblea de silicio maniquí.
- Quitar la cera restante, la fotoprotección y los colgantes Cr / Au capas en los bordes de las lentes utilizando ultrasonidos durante 1 hr utilizando N-metil-2-pirrolidona como disolvente a 80 ° C en un tanque ultrasónico.
- Crear un molde réplica de PDMS de las microlentes fabricados en las fotomáscaras 11.
- Caracterizar las dimensiones fotomáscaras (longitud y anchura) y el molde microlentes PDMS (profundidad y el diámetro) réplicas utilizando un microscopio electrónico de barrido y microscopio estereoscópico respectivamente 12-14.
2. Ejes MN Fabrication
- Crear una cavidad de 2,5 cm x 0,9 cm utilizando los portaobjetos de vidrio montadas en ambos lados de un vaso. El número de los portaobjetos de vidrio apiladas en ambos lados determinará la altura de la cavidad conocida como espesor del espaciador (Figura 1B).
- Asegure cada capa de la lámina de vidrio mediante la aplicación de una capa delgada de la solución de prepolímero que contiene poli (etilenglicol) diacrilato (PEGDA, MW = 258 Da) con 0,5% w / w 2-hidroxi-2-metil-propiofenona (HMP) en el portaobjetos de vidrio seguido de irradiación de la luz creado con la alta intensidad ultravioleta (UV) durante 2 segundos.
- Coloque el Photomask (previamente fabricado) con las superficies de Cr / Au recubiertas que enfrenta el interior de la cavidad. Asegúrese de que los lados de las paredes de la cavidad no están ocultando las lentes incrustadas en la fotomáscara.
- Llenar la cavidad con la solución de prepolímero hasta que la superficie revestida Cr / Au se encuentra en contacto con la solución sin burbujas visibles.
- Irradiar la configuración con alta intensidad de luz UV de una intensidad deseada durante 1 segundo a una distancia de 3,5 cm desde la fuente de UV utilizando la estación de curado UV con una gama de filtros UV de 320-500 nm. Utilice un adaptador de colimación con la sonda de la luz UV.
- Medir la intensidad de la luz UV se utiliza mediante un radiómetro.
- Después de la exposición UV, retire la fotomáscara con el conjunto de los MNs. Vierta la solución de prepolímero exceso que no se polimeriza en el proceso de nuevo en su envase original para reutilizarlo.
- Cuantificar la longitud y el diámetro de la punta el MNS utilizando un estereomicroscopio de acuerdo con las instrucciones del fabricante.
- Con unas pinzas, coloque el MNS (previamente fabricado) conectados a la fotomáscara en un pocillo de una placa de 24 pocillos como se muestra en la Figura 1C.
- Añadir un volumen especificado (300 - 400 l) de la solución de prepolímero en el pozo hasta que las agujas están sumergidos a una altura deseada. Este volumen determina el espesor de la capa de soporte resultante.
- Irradiar la instalación con luz de alta intensidad UV (15,1 W / cm 2), 10,5 cm de distancia de la fuente de UV con una duración de 1 seg.
- Separar la capa de soporte de la matriz de MN de la fotomáscara usando una cuchilla afilada.
- Cuantificar la longitud, el diámetro de la punta y la base de diámetro de los los MNs con la capa de respaldo utilizando un estereomicroscopio de acuerdo con las instrucciones del fabricante.
Subscription Required. Please recommend JoVE to your librarian.
Representative Results
La geometría de los los MNs puede verse afectada de manera significativa por las características fotomáscaras y microlentes incrustadas. El grado de refracción afecta la ruta de transmisión de los rayos UV, que influyeron en la geometría MN (Figura 2). Cada microlente se encontró que tenía un diámetro de 350 micras, 130 micras un aplanados superficie convexa, y un 62,3 micras de profundidad (Figura 2B-D). Usando el teorema de Pitágoras, el radio de curvatura de la primera superficie se encontró que era 272,89 m. La longitud focal se calculó que era 509,28 m (considerando n = 1,53627 vidrio; n = 1.000 aire; λ = 365 nm) a través de la ecuación fabricante de lentes 12 como se indica a continuación:
1 / f = (n 1 / n m -1) * (1 / r -1 1 / r 2)
Donde n 1 es el índice de refracción del material de la lente, n m es el índice de refracción del medio ambiente, r 1 es el radius de curvatura de la primera superficie, y r 2 es el radio de curvatura de la segunda superficie.
El efecto de la intensidad de los rayos UV de la longitud MN, la nitidez y la deformación estructural se estudió mediante la variación de la intensidad de la luz UV 3,14 hasta 15,1 W / cm 2 a una distancia focal constante y la distancia fuente de luz. Se encontró que la longitud media MN aumentó significativamente (p <0,05) con el aumento de intensidad a partir de 3,14 a 9.58 W / cm 2 (Figura 3A). Nuevos aumentos en la intensidad de hasta 15,1 W / cm 2 no produjeron cambios significativos en la longitud. El diámetro de la punta (medida de la nitidez) y la estructura de punta MN se encontraron a variar con el aumento de la intensidad (Figura 3B). Se observaron el MNS con una forma regular y sin ninguna deformación estructural en 6,4 W / cm2.
La capa de soporte se fabricó para permitir la eliminación de MN en forma de un parchey para hacer que el reutilizable fotomáscara. También proporcionó la fuerza a los ejes MN. Por lo tanto, también se estudió el efecto del volumen capa de soporte (el volumen de las disoluciones del prepolímero para formar la capa de espalda). Con diámetros de punta no afectados, se observaron el MNS con una gama de la longitud (1.336 ± 193 m para 300 l y 957 ± 171 m para 400 l) después de la exposición UV (Figura 4).
Figura 1. (A) Representación esquemática del proceso de fabricación de lentes fotomáscara embebidos. (1) 4 "oblea de vidrio. (2) Cr / Au capa depositada usando un evaporador de haz de electrones. (3) La exposición de Cr capa de máscara / Au / resina fotosensible a la luz UV con fotomáscara. (4) La formación de patrón en capa usando Cr / Au grabador. (5) la unión temporal de vidrio sobre una oblea de silicio maniquí. (6) - (7) Grabado húmedo (isotrópica) proceso utilizando reactivos de ataque HF / HCl seguido por ultrasonicación. (8) Desconsolidación de oblea de silicio maniquí y la eliminación de la capa de resina fotosensible. (B) Representación esquemática del proceso de fabricación de agujas. Fotomáscara recubierto de cromo (9 x 9 arrays), se coloca sobre una cavidad que contiene solución de pre-polímero y expuesto a UV. (C) Representación esquemática del proceso de fabricación de la capa de soporte. Fotomáscara, con microagujas adjuntos, se coloca en un pozo lleno de pre-polímero y se expone a los rayos UV. Haga clic aquí para ver una versión más grande de esta figura.
Figura 2. Caracterización de fotomáscara. (A) la exposición UV enfoca la luz en una conica l camino, produciendo los MNs cónicos. (B) y una imagen SEM de una microlente (C). (D) Una porción de un conjunto de réplicas del molde de PDMS copiados de las microlentes, que muestra la superficie convexa aplanada, bajo un estereomicroscopio. (E) Un fotomáscara que muestra el patrón. Haga clic aquí para ver una versión más grande de esta figura.
Figura 3. Efecto de los parámetros de UV en la geometría de microagujas. Efecto de (A) Intensidad y (B) Espesor espaciador de la duración de microagujas. Haga clic aquí para ver una versión más grande de esta figura.
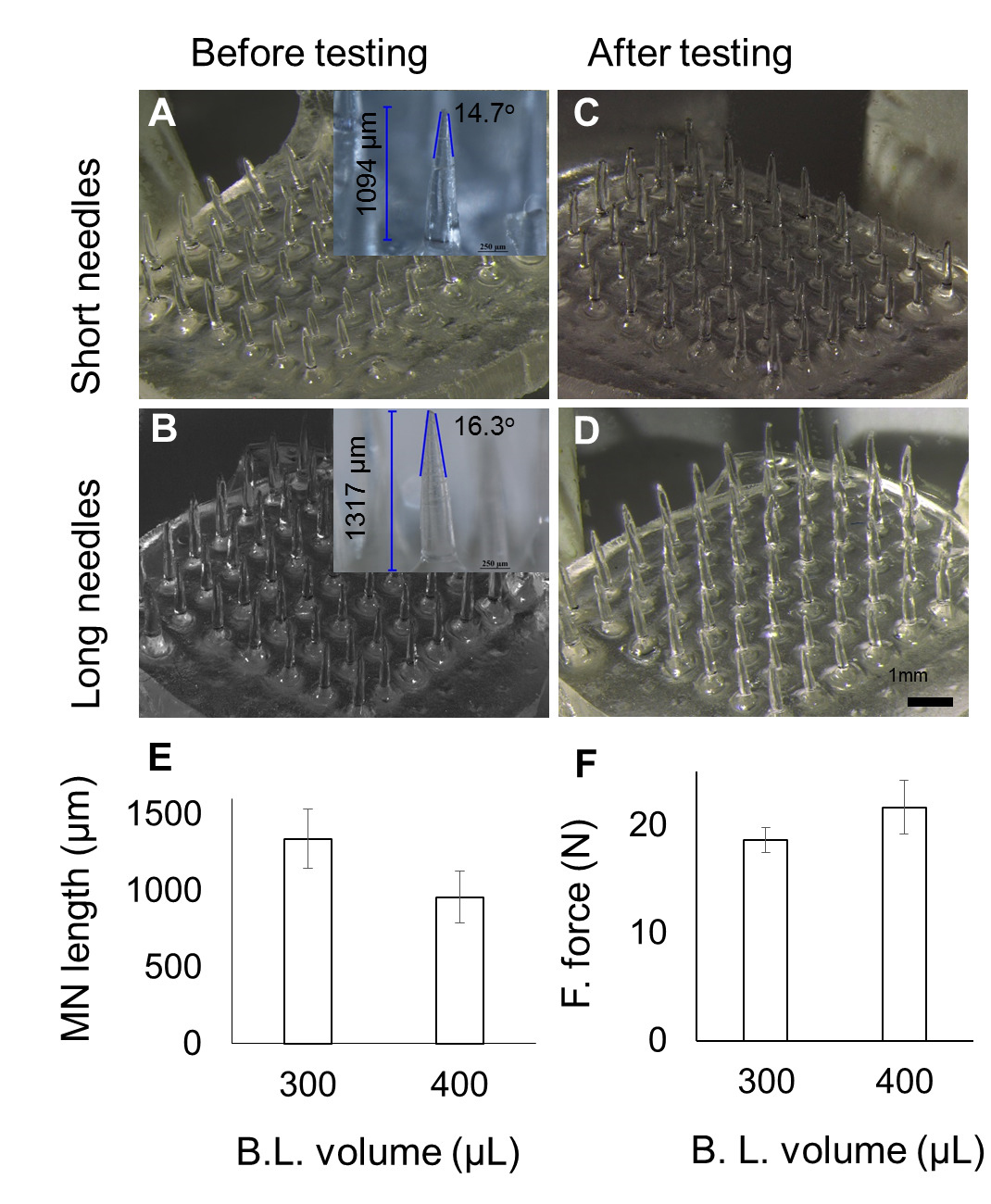
Figura 4. Efecto de la variación de volumen de pre-polímero utilizado para la fabricación de capa de refuerzo. (A - B) en las varias imágenes de volumen, con una longitud promedio MN para cortos (957 m) y largos (1,336 M) MNs. (C - D) Imágenes correspondientes a (AB) después de la prueba de fuerza de fractura. (E) disminución de la longitud MN con aumento de volumen utilizado para la fabricación de la capa de soporte. Fuerza de fractura (F) MN través de los dos volúmenes anteriores a polímeros usados para fabricar la capa de soporte (BL). Haga clic aquí para ver una versión más grande de esta figura.
Subscription Required. Please recommend JoVE to your librarian.
Discussion
El protocolo descrito anteriormente para la fabricación de la matriz de los MNs se ha presentado para la fabricación de la matriz de los MNs ~ 1 cm 2. Las matrices se pueden ampliar mediante la creación de una cavidad de tamaño grande y mediante el uso de una fotomáscara más grande. El aumento del tamaño de la cavidad se puede crear mediante el aumento de la anchura entre los espaciadores a cada lado. Aunque cada paso para fabricar las matrices MN en el protocolo era importante, los pasos más importantes fueron: el posicionamiento fotomáscara, el relleno de la solución de prepolímero, y la irradiación de la configuración. Posicionamiento de la fotomáscara debe ser de tal manera que las superficies de Cr / Au recubiertas se enfrentan al interior de la cavidad y los lados de las paredes de la cavidad oscurecer las lentes incrustadas en la fotomáscara. Al llenar el molde con la solución de prepolímero, asegurar que el aire burbujas no se atrapan que de lo contrario puede dar lugar a una matriz MN fuerza deforma y baja. Las burbujas de aire se pueden prevenir a través de una acción de absorción controlada añadiendo lentamente el prepolymesolución de r y asegurar que no haya burbujas de aire presentes en la solución de prepolímero. Posicionamiento de la configuración para la irradiación debe hacerse de una manera guiada para asegurar la exposición UV uniforme. Antes de la exposición a la luz ultravioleta, la configuración se ajusta y se coloca dentro de la demarcación en el soporte base.
El MNS formados usando fotolitografía fueron muy influenciadas por la presencia de los micro-lentes como la lente resultó en la polimerización en un camino convergente, que condujo a la formación de las más nítidas los MNs en comparación con los los MNs cilíndricas formadas usando la fotomáscara planar. En la fotomáscara plana, la luz UV pasa a través de él con poca desviación (casi en línea recta) que resulta en la formación de los los MNs cilíndricos con puntas afiladas menos. Mientras que en la fotomáscara de microlentes embebido, la luz UV que pasa a través de las lentes se sometieron a la refracción y convergentes, lo que resulta en la formación de los MNs de punta afilados. La ecuación del fabricante de lentes que se ha utilizado como un predictive modelo para aproximar la longitud de la MN mediante la correlación con la longitud focal de las microlentes dio una predicción de la longitud tres veces menor que la real. La discrepancia puede deberse a la superficie convexa aplanado de la microlente, que no permiten refracción de la luz como la lente convexa convencional. 13
Otro factor para la geometría MN fue la intensidad de la luz UV. La intensidad de 6,44 W / cm 2 fue elegido porque las agujas producidas a esta intensidad poseían resistencia mecánica suficiente para aplicaciones de piel. Otro hallazgo relacionado con la intensidad era que, con cada incremento en la intensidad UV, la longitud de MN aumenta. Esto podría ser atribuido a la parte superior plana de la microlente, que permitió a algunos de los rayos de luz para viajar más allá del punto focal. 14,15 Además, el grado de polimerización tiene su límite, en función de la ley de la inversa del cuadrado de la luz, es decir, la luz pierde energía como la distancia de distanciade la fuente aumenta. 16
Los protocolos descritos aquí tienen la ventaja de la fabricación libre de moho dentro de un corto período de tiempo. Pero no podemos predecir hasta dónde se puede tomar aún más para la fabricación a granel. Los MNS arreglos fueron hechos de un polímero biocompatible de bajo coste. Potencialmente se puede utilizar como dispositivo de administración transdérmica de fármacos para aplicaciones farmacéuticas y cosméticas. Más interesante, que puede ser utilizado como una combinación del sistema de suministro y el dispositivo, como los compuestos terapéuticos pueden ser encapsulados (por mezcla o solubilizante en solución de prepolímero) durante la fabricación de MNs. 5,6,17 La solubilidad del compuesto añadido dentro de la solución de prepolímero se debe tomar en consideración como las características MN, por ejemplo, resistencia MN, puede. cambiar 17
Subscription Required. Please recommend JoVE to your librarian.
Materials
Name | Company | Catalog Number | Comments |
Poly(ethylene glycol) diacrylate (PEGDA Mn=258) | SIGMA | 475629-500ML | |
2-hydroxy-2-methyl-propiophenone (HMP) | SIGMA | 405655-50ML | |
Bovine collagen type 1, FITC conjugate | SIGMA | C4361 | |
UV curing station | EXFO Photonic Solutions Inc., Canada | OmniCure S2000-XL | |
Collimating Adaptor | EXFO Photonic Solutions Inc., Canada | EXFO 810-00042 | |
24-well plate | Thermo Fisher Scientific, USA | ||
Nikon SMZ 1500 stereomicroscope | Nikon, Japan | ||
Dillon GL-500 digital force gauge | Dillon, USA | ||
A-1R confocal microscope | Nikon, Japan |
References
- Zhou, C. P., Liu, Y. L., Wang, H. L., Zhang, P. X., Zhang, J. L. Transdermal delivery of insulin using microneedle rollers in vivo. International journal of pharmaceutics. 392, 127-133 (2010).
- Lee, J. W., Choi, S. O., Felner, E. I., Prausnitz, M. R. Dissolving microneedle patch for transdermal delivery of human growth hormone. Small. 7, 531-539 (2011).
- Raphael, A. P., et al. needle-free vaccinations in skin using multi layered, densely-packed dissolving microprojection arrays. Small. 6, 1785-1793 (2010).
- Lee, J. W., Han, M. R., Park, J. H. Polymer microneedles for transdermal drug delivery. Journal of drug targeting. 21, 211-223 (2012).
- Kochhar, J. S., Goh, W. J., Chan, S. Y., Kang, L. A simple method of microneedle array fabrication for transdermal drug delivery. Drug development and industrial pharmacy. 39, 299-309 (2013).
- Kochhar, J. S., Zou, S., Chan, S. Y., Kang, L. Protein encapsulation in polymeric microneedles by photolithography. International journal of nanomedicine. 7, 3143-3154 (2012).
- Tay, F. E. H., Iliescu, C., Jing, J., Miao, J. Defect-free wet etching through pyrex glass using Cr/Au mask. Microsystem Technologies. 12, 935-939 (2006).
- Iliescu, C., Chen, B., Miao, J. On the wet etching of Pyrex glass. Sensors and Actuators, A: Physical. 143, 154-161 (2008).
- Iliescu, C., Taylor, H., Avram, M., Miao, J., Franssila, S. A practical guide for the fabrication of microfluidic devices using glass and silicon. Biomicrofluidics. 6, 16505-16516 (2012).
- Iliescu, C., Jing, J., Tay, F. E. H., Miao, J., Sun, T. Characterization of masking layers for deep wet etching of glass in an improved HF/HCl solution. Surface and Coatings Technology. 198, 314-318 (2005).
- Pan, J., et al. Fabrication of a 3D hair follicle-like hydrogel by soft lithography. Journal of biomedical materials research. Part A. 101, 3159-3169 (2013).
- Jay, T. R., Stern, M. B. Preshaping photoresist for refractive microlens fabrication. P Soc Photo-Opt Ins. 1992, 275-282 (1993).
- Friedman, G. B., Sandhu, H. S. Longitudinal Spherical Aberration of a Thin Lens. Am J Phys. 35, 628 (1967).
- Xu, Q. A., Li, J., Zhang, W. Collimated the laser diode beam by the focus lens. Semiconductor Lasers and Applications IV. 7844, (2010).
- Lin, T. W., Chen, C. F., Yang, J. J., Liao, Y. S. A dual-directional light-control film with a high-sag and high-asymmetrical-shape microlens array fabricated by a UV imprinting process. J Micromech Microeng. 18, (2008).
- Dunne, S. M., Millar, B. J. Effect of distance from curing light tip to restoration surface on depth of cure of composite resin. Prim Dent Care. 15, 147-152 (2008).
- Kochhar, J. S., et al. Microneedle integrated transdermal patch for fast onset and sustained delivery of lidocaine. Molecular pharmaceutics. 10, 4272-4280 (2013).
- Kochhar, J. S., et al. Direct microneedle array fabrication off a photomask to deliver collagen through skin. Pharmaceutical research. 31, 1724-1734 (2014).