Summary
El aislamiento de los efectos eléctricos y térmicos sobre la deformación asistida eléctricamente (EAD) es muy difícil utilizando muestras macroscópicas. Se han desarrollado micro y nanoestructuras de muestras metálicas junto con un procedimiento de prueba personalizado para evaluar el impacto de la corriente aplicada sobre la formación sin calentamiento de joule y la evolución de las dislocaciones en estas muestras.
Abstract
La deformación asistida eléctricamente (EAD) se utiliza cada vez más para mejorar la formabilidad de metales durante procesos tales como laminación de chapa y forja. La adopción de esta técnica se está llevando a cabo a pesar del desacuerdo sobre el mecanismo subyacente responsable de EAD. El procedimiento experimental descrito en este documento permite un estudio más explícito comparado con la investigación previa de EAD mediante la eliminación de los efectos térmicos, que son responsables del desacuerdo en la interpretación de resultados previos de EAD. Además, como el procedimiento descrito aquí permite la observación EAD in situ y en tiempo real en un microscopio electrónico de transmisión (TEM), es superior a los métodos post mortem existentes que observan los efectos EAD después del ensayo. Las muestras de ensayo consisten en una lámina de cobre de un solo cristal (SCC) que tiene una sección de prueba de tracción independiente de espesor nanométrico, fabricada usando una combinación de láser y fresado de haz de iones. El SCC está montado en una base de silicio grabada que me proporcionaSoporte mecánico y aislamiento eléctrico mientras sirve como disipador de calor. Utilizando esta geometría, incluso con alta densidad de corriente (~ 3.500 A / mm 2 ), la sección de prueba experimenta un aumento de temperatura insignificante (<0.02 ° C), eliminando así los efectos de calentamiento Joule. El control de la deformación del material y la identificación de los correspondientes cambios en microestructuras, por ejemplo , dislocaciones, se realizan mediante la adquisición y el análisis de una serie de imágenes TEM. Nuestros procedimientos de preparación de muestras y de experimentos in situ son robustos y versátiles, ya que pueden utilizarse fácilmente para probar materiales con diferentes microestructuras, por ejemplo , cobre simple y policristalino.
Introduction
La deformación asistida eléctricamente (EAD) es una herramienta útil para procesos de deformación de metales tales como forja, estampado, extrusión, etc. El proceso EAD consiste en aplicar una corriente eléctrica a través de una pieza de trabajo metálica durante la deformación, mejorando significativamente la formabilidad del metal reduciendo las tensiones de flujo, aumentando las deformaciones hasta el fallo ya veces eliminando el resorte elástico después de la formación 1 , 2 , 3 . A pesar de su crecimiento en el uso, no hay consenso en cuanto al mecanismo por el cual EAD mejora la formabilidad del metal. Este artículo describe la preparación de muestras y el procedimiento de prueba para un experimento en el que es posible aislar mecanismos EAD potencialmente competidores y permitir el examen microestructural in situ durante las pruebas.
Hay dos hipótesis para el efecto de EAD sobre la formación de metales. La primera hipótesis, el efecto de calentamiento Joule, staQue la corriente aplicada encuentra resistencia eléctrica en el metal formador, haciendo que la temperatura aumente y conduzca al ablandamiento y expansión del material. Una segunda hipótesis se denomina electroplasticidad, en la que la corriente eléctrica aumenta la deformación al disminuir la energía de activación de la dislocación. Ambas hipótesis surgieron a partir de experimentos realizados en la década de los setenta que involucraron pulsos de corriente de corta duración aplicados a deformar mecánicamente metales 4 , 5 . Estudios más recientes suelen implicar pulsos de DC de menor intensidad, que son más relevantes para las aplicaciones de fabricación, pero los investigadores siguen en desacuerdo en su interpretación de los datos de EAD.
La interpretación de datos EAD es difícil debido a la naturaleza altamente acoplada de la corriente eléctrica aplicada y el aumento de la energía térmica. Incluso pequeñas densidades de corriente en metales altamente conductores pueden aumentar significativamente la temperatura del material; Por ejemplo , 130-240 ° C con una densidad de corriente de 33 - 120 A / mm2 para varias aleaciones de aluminio y de cobre 6 , 7 , 8 , 9 . Este cambio de temperatura puede afectar significativamente el módulo de elasticidad, la resistencia a la deformación y el estrés de flujo, lo que dificulta distinguir entre efectos térmicos y de electroplasticidad. Destacando esta dificultad, se pueden encontrar estudios recientes apoyando la hipótesis de calentamiento de Joule o la hipótesis de electroplasticidad. Por ejemplo, estudiando la deformación electro-mecánica en varias aleaciones de aluminio, cobre y titanio, los investigadores han informado de que la electroplasticidad contribuyó a la deformación mejorada porque el efecto no podía explicarse por la calefacción de Joule solo 1 , 6 , 7 . En contraste con estos informes se encuentran estudios que atribuyen la reducción de estrés EAD en tItanium, acero inoxidable y Ti-6Al-4V a los efectos térmicos 10 , 11 .
La gestión térmica no es específica de la investigación de EAD, sino que es una preocupación general cuando se investigan las propiedades de los materiales electromecánicos. Especialmente en especímenes grandes, donde el centro de masa está profundamente aislado de su entorno, mantener una temperatura uniforme puede ser un reto. Otro desafío de pruebas electromecánicas relacionado con el tamaño de la muestra es la capacidad de realizar observaciones in situ y en tiempo real de cambios microestructurales fundamentales relacionados con el estrés electromecánico. Las pruebas mecánicas TEM in situ se realizan rutinariamente en muestras de ensayo estándar 12, pero la sección transversal no uniforme de las muestras crearía variaciones dependientes de la geometría en la densidad de corriente y la transferencia de calor cerca de la sección del medidor. En resumen, los principales retos en la observación e interpretación de EA D se relacionan con el tamaño de la muestra y se pueden resumir de la siguiente manera: 1) el acoplamiento termoeléctrico influye en la temperatura de la muestra, lo que dificulta aislar un único mecanismo EAD propuesto y 2) no existen muestras y procedimientos estándar para un análisis in situ , en tiempo real Estudio de un material en tensión bajo una corriente eléctrica aplicada. Superar estos retos es posible mediante la realización de experimentos EAD en una muestra con una sección de calibre de volumen ultra bajo en un microscopio electrónico de transmisión (TEM) mientras se controla la corriente eléctrica, la carga mecánica y la temperatura.
En este artículo describimos el procedimiento de preparación y prueba de muestras para un experimento EAD en el que los efectos de calentamiento Joule se hacen insignificantes utilizando una estructura de muestra con una sección de calibre micro / nanoescala (10 μm x 10 μm x 100 nm) Marco de soporte estabilizador. A través de modelos analíticos y numéricos, se ha demostrado(-3.500 A / mm 2 ) resultó en muy poco aumento de la temperatura de la muestra (<0.02 ° C.) Un esquema tridimensional del sistema de prueba electromecánico basado en microdevice (MEMTS) se muestra en la Figura 1. Otra ventaja importante del método presentado aquí es que en lugar de examinar muestras post-prueba, como se hace a menudo 14 , la estructura de la muestra y el marco de soporte están diseñados para encajar directamente en un microscopio electrónico de transmisión TEM) equipado con la capacidad de aplicar simultáneamente cargas mecánicas y eléctricas.Esta configuración permite la observación in situ en tiempo real de la deformación del material a una resolución de nano a nivel atómico.Aunque se utilizan muestras de cobre de un solo cristal para el procedimiento descrito aquí , El método es suficientemente flexible para ser aplicado a otros especímenes de materialMetales, cerámicas y polímeros 15 , 16 .
Protocol
1. Microfabricación de Marcos Si
- Revestimiento de revestimiento (3,000 rpm y 30 s) SPR220-7 fotorresist (PR) en una oblea de Si de 180 μm de espesor. Use suficiente PR para cubrir completamente la oblea. La orientación del plano de cristal de la oblea no es importante.
- Cocción suave de la oblea con una capa de PR (aproximadamente 7,5 μm de grosor) a 60 ° C durante 2 min y luego a 115 ° C durante 90 s sobre una placa caliente.
- Exponer la capa de PR a la luz ultravioleta a través de una fotomáscara de cromo / vidrio con patrón que permite que la luz pase a través de ella para definir la forma del marco de Si. Utilizar equipos y procesos de fotolitografía estándar para este paso y el siguiente ( Figura 2a-b ).
- Desarrollar los patrones expuestos a través de la fotomáscara sumergiendo la oblea de Si con PR en ella en MF 24A o MF 319 sin diluir durante aproximadamente 1 minuto ( Figura 2c ). La capa PR modelada sirve como máscara durante el paso 1.6.
- Unir la oblea de Si de 180 μm de espesor a una tolva de Si de soporte de 500 μm de espesorR utilizando un adhesivo temporal de punto de fusión bajo para una manipulación más sencilla (vea la Tabla de Materiales para más detalles). Caliente el adhesivo en un plato de vidrio usando una placa caliente (70 ° C) y use el adhesivo suficiente para cubrir la oblea de soporte. A continuación, presione ligeramente la oblea de Si de 180 μm de espesor sobre la oblea de 500 μm de espesor ( Figura 2d ).
- Grabado a presión a través de la oblea de silicio superior desde arriba para hacer estructuras libres. Utilice cualquier número de sistemas de grabado de iones reactivos de plasma acoplados inductivamente disponibles comercialmente que utilicen el proceso Bosch con gases SF6 y C4F8 para la etapa de grabado. En el proceso de Bosch, los ciclos alternos de la deposición de la capa de pasivación y el grabado por plasma dan lugar a trincheras profundamente grabadas con paredes laterales casi intactas) (Figura 2e).
- Comenzar con 3 y 100 sccm flujos de SF 6 y C 4 F 8 durante 5 s durante la deposición y 100 y 2,5 sccm de SF 6 y C 4 F
- Cada 20 minutos, mida la profundidad de la zanja grabada utilizando un perfilómetro para calibrar la velocidad de grabado que es específica para los instrumentos y la receta de grabado.
- Desconecte la oblea de Si de soporte y limpie la oblea de Si delgada removiendo el adhesivo temporal y PR usando un remojo de acetona durante la noche ( Figura 2f ). A continuación, enjuague bien la oblea fina con agua desionizada (DI).
- Depósito de una capa de aislamiento de SiO 2 a 300 ° C a ambos lados del marco de Si utilizando cualquier sistema de deposición química en fase de vapor (PECVD) comercialmente disponible con gases SiH 4 , N 2 O y N 2 ( Figura 2g ). Utilizar recetas de deposición de SiO2 estándar, por ejemplo , usar 5% de SiH4 a 170 sccm y N2O a 710 sccm, Para depositar una capa de SiO2 de 2-3 μm de espesor.
- Romper las lengüetas que conectan los marcos rectangulares individuales del Si a las estructuras circundantes. Utilice pinzas afiladas bajo un microscopio óptico ( Figura 2h ).
2. Modelado láser de especímenes metálicos
- Cortar un pedazo de lámina de cobre de 5.0 cm x 5.0 cm (99.99% de pureza, ver tabla de materiales ) y adherirlo con cinta adhesiva a un portaobjetos de vidrio. Revuelva los dos lados con una capa de PR de 1 μm de espesor. Mientras que una lámina con un amplio intervalo de espesor (hasta 100 μm) puede ser cortada por las técnicas de láser, aquí se utilizan dos grosores diferentes (13 μm y 25 μm) para la demostración. Use suficiente PR para cubrir completamente las superficies. Hornear el PR a 115 ° C durante 2 min. El PR es necesario para proteger la superficie de la lámina de cobre de los desechos producidos durante la etapa de corte por láser y para permitir el ataque químico de los haces de muestra (véase el paso 2.4) sin afectarE superficie de la lámina.
- Utilizando un láser pulsado Nd: YVO 4 de 355 nm, 10 vatios, de estado sólido, triplicado en frecuencia a 50 kHz con un ancho de impulso de ~ 90 ns, se corta un conjunto de 5 por 4 especímenes individuales, cada uno de ellos sujetado por un armazón de cobre de 4 mm de largo por 1 mm de ancho ( Figura 3b ).
- Ajuste el rayo láser a una fluencia de 65 mJ / cm2 en la superficie de la lámina de cobre. Esto proporciona suficiente energía láser para cortar el cobre en dos pasadas sin calentamiento excesivo y / o daño del cobre adyacente. El patrón para cada espécimen es generado por un espejo de exploración de Galvo que escanea el rayo láser para cortar la lámina de cobre generando 20 especímenes a la vez ( Figura 3a ). Ajuste el ancho del haz de muestras cortadas con láser de 30 μm (para la lámina de 13 μm de grosor) a 50 μm (para la lámina de 25 μm de grosor).
- Grabe químicamente el conjunto de muestras sumergiéndolo en cloruro férrico líquido al 40% a 40-60 ° C durante 30 s (para la lámina de 13 μm de espesor) o 40 s (para t) Para eliminar los bordes de corte láser potencialmente dañados, reducir la anchura de los haces individuales de muestra por debajo de 20 μm ( Figura 3c ) y producir un perfil de borde de viga suave.
- Quitar la fotorresistencia protectora sumergiendo las matrices en baños disolventes separados de la primera acetona, luego metanol seguido de isopropanol y luego se seca con nitrógeno. Almacene las matrices de muestras en un desecador de nitrógeno seco. En la figura 3d se muestra un esquema transversal de las etapas de fabricación anteriores.
- Utilice el láser para cortar una caja alrededor de la matriz de muestras, liberándola del resto de la lámina de cobre.
3. Ensayos de Ensamble e In Situ TEM
- Separar una muestra individual (incluyendo su marco de cobre) usando mini-tijeras. Coloque una pequeña cantidad de epoxi de plata en el marco de silicio y cuidadosamente alinear la muestra bajo un microscopio óptico para que el medidor de muestra abarca la estrecha brecha en el centro de laE marco ( Figura 4a ).
- De forma similar a la Etapa 3.1, conecte alambres de plata (50 μm de diámetro) a ambos extremos de la muestra por epoxi de plata ( Figura 5c ).
- Utilice fresado de haz de iones enfocado (FIB) para crear la sección de calibre de nanoescala (100 nm x 10 μm x 10 μm) con múltiples hombros. Las secciones transversales progresivamente más gruesas que se alejan de la sección de calibre están diseñadas para producir una transición suave en densidades de corriente, una densidad de corriente más uniforme en la sección de medida y para minimizar el calentamiento localizado en cualquier hombro dado. Para minimizar el daño, utilice tensión de aceleración reducida (5 kV) y corriente (<80 pA) durante la molienda final de muestras de cobre. Medir el área de la sección transversal del calibre utilizando microscopio electrónico de barrido (SEM) imágenes ( Figura 4b-e y 5b ).
- Retire los fotogramas del espécimen, ya sea por corte con láser, FIB, o mini-tijeras (vea el recuadro de la Figura 4a ). Aunque no es el caso en la imagen, la ubicación oF el corte idealmente debe estar alejado de la sección del medidor para minimizar el posible daño material a la sección del medidor.
- Monte los MEMTS en un solo soporte de TEM (ver Tabla de Materiales ) bajo un microscopio óptico y luego conéctelo usando pernos y arandelas no conductoras. Las arandelas se utilizan para evitar la torsión no deseada durante el montaje. Utilice arandelas de 0,5 mm de espesor modeladas a partir de una lámina de fibra eléctrica de fibra dura utilizando un sistema de láser de CO2 de 50 W (consulte la Tabla de materiales para parámetros específicos durante el corte con láser).
- Conecte los alambres de plata de la Etapa 3.2 a los pasadores metálicos ( Figura 5a ) en el soporte de TEM usando epoxi de color plateado.
- Utilizando un multímetro de mano o de escritorio, compruebe la resistencia a través de los MEMTS (B y C en la Figura 1 ) para verificar que la sección del medidor no esté rota. La resistencia debe ser inferior a 100 Ω. También mida la resistencia entre el MEMTS y el soporte del espécimen TEM con conexión a tierra para confirmar que no hay interferencia eléctrica entre la muestra y el soporte TEM. Si la muestra está aislada, la resistencia medida debe ser mayor de 10 MΩ.
- Coloque el soporte TEM con el MEMTS en el TEM para experimentos in situ .
- Conecte una fuente de alimentación de CC externa (vea la Tabla de Materiales ) a las entradas eléctricas incorporadas en el soporte de TEM para aplicar señales de entrada de CC a la muestra desde fuera de la cámara de TEM para el control de la corriente eléctrica. Las ubicaciones de conexión eléctrica dependerán de los fabricantes de los terminales TEM, pero para este estudio, las conexiones se localizaron en la manija del soporte y se usaron conectores de clavija para aplicar alimentación desde el suministro a los especímenes TEM. Obtener la densidad de corriente nominal en la sección de calibre dividiendo la corriente de entrada por el área de la sección transversal (obtenida a partir de una imagen de SEM en la figura 5b ).
NOTA: La inclinación simpleEl soporte TEM contiene un actuador incorporado que es controlado por un controlador de desplazamiento separado ( Tabla de Materiales ). - Mientras controla la carga mecánica y eléctrica, adquiera las imágenes TEM durante los pasos que siguen. También se pueden utilizar otras tensiones y cargas de corriente.
- Aplicar la deformación de tracción gradualmente en pequeños pasos dependiendo de la resolución del actuador piezo integrado (~ 0.34 nm en este ejemplo) hasta que se observen movimientos de una o varias dislocaciones al mismo tiempo. Este es un paso crucial para que cualquier aumento adicional en la energía térmica y / o eléctrica produzca movimiento adicional.
- Deje que la muestra se equilibre durante un minuto.
- Aplique una densidad de corriente de entrada a la muestra. Debido a la pequeña sección transversal, la corriente debe ser suficientemente baja, incluso a grandes densidades de corriente, para que no produzca un aumento significativo de la temperatura (
EnCalibre la sección. El aumento de la temperatura máxima en el centro de la sección del medidor depende de la geometría de la muestra y de las propiedades del material como se describe a continuación.
- Para visualizar una muestra en estado estacionario, manténgala bajo el haz de electrones durante un minuto mientras mantiene la corriente constante antes de adquirir imágenes. Permitir que la muestra se equilibre de esta manera se aplica después de cualquier cambio en la carga mecánica o eléctrica.
Representative Results
Preparación y ensayo como se describió anteriormente debe resultar en un espécimen que fracturas en su indicador, similar a la muestra de cobre de cristal único (SCC) que se muestra en la Figura 6 a . La falla mecánica debe ir acompañada de un gran aumento en la resistencia, lo que confirma que el espécimen de SCC está aislado eléctricamente por las arandelas aisladas y el marco de silicio recubierto de óxido. Las dislocaciones planas en la muestra deben observarse usando el modo de campo brillante de TEM enfocado cerca de un eje de zona. Al incrementar gradualmente la tensión hasta alcanzar el estrés de flujo (el estado de equilibrio post-rendimiento), los movimientos de dislocación deben ser visibles ( Figura 6b ). Con una tensión adicional y / o una corriente aplicada, los movimientos de dislocación correspondientes pueden monitorizarse continuamente.
FiguraLa figura 7 muestra imágenes representativas durante un experimento EAD en una muestra 13 de SCC. Después de forzar la muestra a su estado de equilibrio post-rendimiento, la deformación adicional se aplicó sin aplicar ninguna corriente (véase la figura 7 b 1 ). Esto dio como resultado un nuevo bucle de dislocación (o posiblemente un segundo deslocamiento de deslizamiento), como se indica por la flecha en la Figura 7 b 2 . Sin modificar la deformación, se aplicó una densidad de corriente de 500 A / mm2, pero esto no produjo movimiento notable en ninguna dislocación ( Figura 7b 3 ). Se retiró la corriente, se mantuvo constante durante un minuto y se aumentó de nuevo la deformación, produciendo nuevamente cambios notables en el bucle de dislocación indicado por la flecha en la figura 7b 4 . Este resultado ilustra el potencial de este procedimiento para aislar los efectos térmicos y eléctricos implicados en la deformación asistida eléctricamente. También se han realizado experimentos que implican mayores densidades de corriente (hasta 5 kA / mm 2 ) utilizando esta técnica, obteniendo resultados similares, sin movimientos de desplazamiento adicionales observables en ausencia de esfuerzo adicional. El uso de densidades de corriente más altas enfatiza la capacidad de esta técnica para eliminar las tensiones térmicas causadas por el calentamiento Joule, que han complicado los conjuntos de datos anteriores de EAD.
Teniendo en cuenta el pequeño tamaño de la sección de calibre de muestra, la elección de un material de alta calidad es de suma importancia. Por ejemplo, los defectos del material de microescala, por ejemplo , huecos, cerca de una sección de calibre resultarían en un fallo catastrófico de una muestra durante la preparación del material ( Figura 4 g ). Esto es particularmente Ya que es difícil saber si hay defectos de material no vistos en la sección del medidor sin realizar ensayos no destructivos adicionales, tales como la topografía por difracción de rayos X. Sin embargo,
Otro desafío clave es el posible daño superficial durante el láser o el fresado de iones enfocados, incluyendo la implantación de iones Ga, las dislocaciones inducidas por el haz de iones y la formación de estructuras amorfas a partir del calentamiento inducido por láser. La mayoría de los artefactos de superficie pueden eliminarse utilizando un proceso de molienda FIB suave (etapa 3.3). Sin embargo, el uso de estas técnicas de microfabricación todavía requiere una consideración cuidadosa ya que estos defectos superficiales podrían alterar las microestructuras de la muestra y influir en gran medida en los resultados experimentales de EAD. En nuestro trabajo, se utilizaron imágenes TEM de alta resolución y patrones de difracción para confirmar que nuestros especímenes eran de hecho cristalino cristalino prístino Figura 6 c .
Contenido "fo: keep-together.within-page =" 1 "> Cabe señalar que el aumento de la temperatura máxima en el centro de la sección del medidor se puede calcular usando la siguiente ecuación 13 :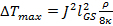





P_upload / 55735 / 55735fig1.jpg "/>
Figura 1: El sistema de prueba electromecánico basado en microdevice (MEMTS). Esta imagen es un esquema tridimensional (3D) que muestra los componentes importantes y cómo los especímenes encajan en el soporte de TEM. Sólo los cables que conectan la muestra a los pines en el soporte de TEM no se muestran. Haga clic aquí para ver una versión más grande de esta figura.
Figura 2: Proceso de fabricación del marco de silicio. Una oblea de Si desnuda ( a ) se recubre por centrifugación con fotorresistencia ( b ), que se moldea a continuación usando fotolitografía. La fotorresistencia expuesta se desarrolla lejos para exponer la oblea de Si ( c ) subyacente. La oblea está temporalmente unida a una oblea de soporte más gruesa y reactivaIon grabado (RIE) se utiliza para grabar a través de la oblea superior delgada ( d - e ). La acetona se utiliza para eliminar la fotorresistencia y separar la oblea de soporte ( f ). Después se deposita una capa de óxido de silicio sobre toda la superficie de la oblea grabada ( g ). Finalmente, los marcos individuales se separan de la oblea tirándolos cuidadosamente de sus lengüetas de soporte ( h ). Haga clic aquí para ver una versión más grande de esta figura.
Figura 3: Fabricación de muestras metálicas. Imágenes ópticas de ( a ) una serie de muestras de cobre ( b ) una muestra individual, y ( c ) una vista de zoom de una sección de calibre. Los pasos del proceso de fabricación se muestran en ( d b ). Ambos lados de una lámina delgada se recubren con material fotorresistente para proteger la muestra durante el corte por láser ( d , arriba). Las estructuras son láser mecanizado ( d , segundo) y luego grabado para producir bordes lisos ( d , tercero). Se pueden producir muchos especímenes a partir de una sola operación de fabricación como se muestra en ( a ). Finalmente, el material fotorresistente se retira y los especímenes individuales se retiran suavemente de la lámina de muestra ( d , parte inferior). Haga clic aquí para ver una versión más grande de esta figura.
Figura 4: Imágenes de fresado de haz de iones enfocados (FIB). La imagen ( a ) muestra la muestra conectada al marco Si y una vista cercana(Inserción) del soporte del espécimen después de que fue cortado con láser. Las imágenes ( b ) - ( e ) muestran que la sección de medida se hace progresivamente más delgada durante sucesivas pasadas FIB. Cada pasada elimina menos material para mejorar el acabado superficial y disminuir los cambios en la propiedad del material debido al proceso de fresado. Sin embargo, es posible que los defectos de sección de calibre permanezcan ( f ), lo que puede dar lugar a un fallo del material incluso antes de que se aplique una deformación ( g ). Haga clic aquí para ver una versión más grande de esta figura.
Figura 5: Modelo montado en un soporte TEM. (A) y ( b ) muestran una muestra ensamblada en un soporte de TEM y una dimensión final de la sección de medida con superficies lisas usando genMolienda FIB. Una vez que el espécimen está unido al marco de Si y los alambres de plata se conectan usando el epoxy conductor ( c ), los dos agujeros circulares en el marco de Si se utilizan para montar el espécimen en el sostenedor de TEM. Se utilizan arandelas no conductoras para aislar la muestra del soporte de TEM. Finalmente, los alambres de plata se unen a los pernos de soporte de TEM usando epoxi conductor. Modificado 13 , con el permiso de AIP Publishing. Haga clic aquí para ver una versión más grande de esta figura.
Figura 6: Una muestra de cobre de cristal único (SSC) representativa. (A) muestra la sección de calibre (posición A de la figura 1 ) tomada después de la falla de la sección de medida. B C ) muestra el patrón de difracción en la sección de calibre. Modificado 13 , con el permiso de AIP Publishing. Haga clic aquí para ver una versión más grande de esta figura.
Figura 7: Imágenes TEM experimentales EAD in situ . Estas imágenes revelan efectos de carga mecánica y eléctrica sobre el movimiento de dislocación. ( B1 ) - ( b4 ) muestran la vista de acercamiento del Área ( b ) en ( a ). ( B1 ) muestra la muestra en un estado de equilibrio post-rendimiento. ( B2 ) identifica la formación del lazo de dislocación resultante de la tensión adicional más allá del estado mostrado en (
Discussion
Micro / nanotecnología ha ofrecido poderosas herramientas para caracterizar el comportamiento del material en cámaras analíticas, incluyendo escaneo 16 , 18 , 19 , 20 , 21 y microscopios electrónicos de transmisión 13 , 22 , 23 , 24 . Tal capacidad de prueba in situ es altamente atractiva para la ciencia de los materiales y la comunidad de ingeniería, ya que las microestructuras fundamentales y los mecanismos de deformación subyacentes se pueden observar directamente utilizando microscopía electrónica de alta resolución [ 25 , 26] .
Aquí presentamos un método basado en microdevice para investigar el comportamiento eléctrico y mecánico acoplado de muestras de material utilizandoAntages de TEM in situ . Los pasos en este enfoque requieren una experiencia media utilizando fotolitografía, equipos de grabado iónico reactivo, microscopios electrónicos, y acceso a un sistema de mecanizado láser de alta calidad como el que se utiliza aquí. Aunque el montaje de los especímenes y los soportes de silicona se realiza utilizando medios simples: epoxi de plata y un microscopio óptico básico, se debe tener cuidado para no dañar la sección del medidor de muestras. Esto es cierto en todo momento cuando se manipula la muestra. También se debe tener cuidado durante los procesos finales de fresado FIB de los especímenes de cobre. La reducción de la tensión de aceleración (5 kV) y de la corriente (<80 pA) 27 durante el pulido final reducirá el posible daño de la muestra 28 y producirá una sección de calibre suave y sin defectos. Otro punto importante a recordar es comprobar que la muestra está aislada eléctricamente del soporte de TEM para asegurar que la corriente aplicada pasa a través de la sección de medidaUna vez que comience el experimento.
El proceso de grabado de obleas incluye algunos pasos que son críticos para fabricar un buen marco para el espécimen EAD. La unión temporal de la oblea de soporte de 500 μm a la oblea de 180 μm con un revestimiento adhesivo temporal uniforme entre las obleas es importante no sólo para ayudar a manejar la oblea grabada frágil, sino que la oblea de soporte facilita también la transferencia de calor durante el proceso de grabado por plasma. Una transferencia de calor insuficiente puede dar como resultado el ataque químico de la máscara de PR y el posterior ataque químico no objetivo del marco de silicio. También es importante medir periódicamente la profundidad de la zanja grabada. La oblea de silicio superior más delgada debe ser completamente grabada, pero debe haber un ataque químico mínimo a la oblea de soporte de modo que pueda actuar como un disipador de calor uniforme a la oblea más delgada. Por último, es importante limpiar a fondo la oblea grabada con acetona seguido de enjuague con agua DI antes de la deposición de SiO2 para minimizar cualquier reSidues
Las imágenes experimentales de EAD que se muestran aquí son representativas de lo que se puede esperar, pero se pueden hacer modificaciones a la resolución, la dosificación y la velocidad de fotogramas para permitir una mejor observación y cuantificación de las dislocaciones. Además, el software de procesamiento de imágenes puede utilizarse para analizar una serie de imágenes TEM con una resolución mejorada.
El MEMTS ofrece varias ventajas únicas para estudiar el comportamiento del material electromecánico. Este sistema permite la observación directa de fenómenos de nanoescala que gobiernan las deformaciones de material macroscópico bajo carga electromecánica. En segundo lugar, las secciones de calibre de muestra con pequeña sección transversal proporcionan la capacidad de aplicar densidades de corriente eléctrica sustanciales usando una magnitud de corriente baja, eliminando así las preocupaciones de seguridad inherentes con el uso de instrumentos de alta potencia. Por ejemplo, la aplicación de una densidad de corriente de 1.000 A / mm2 a una sección de 1 mm 2 requeriría 1 kA en comparación con sólo1 mA si la sección transversal del medidor se redujo a 1 μm 2 . Más importante aún, el uso de una corriente más baja ayuda en el manejo térmico. El MEMTS es también único en que su alineación y montaje no requieren equipos costosos y no requieren mucho tiempo en comparación con otros métodos de montaje basados en microdevice.
El método descrito aquí se presta bien a las pruebas electromecánicas de metales, cerámicas y polímeros, pero también puede usarse para explorar el comportamiento electromecánico dependiente de la microestructura dentro de cada una de esas clases de materiales. Por ejemplo, el impacto de la monocristalinidad y la policristalinidad, la orientación del grano, el tamaño del grano, la distribución de fases y la densidad de defectos en el comportamiento electromecánico podrían investigarse preparando muestras representativas. Los conocimientos obtenidos de un estudio tan amplio podrían proporcionar la comprensión necesaria para comprender mejor el (los) mecanismo (s) de conducción de EAD y avanzar las capacidades de fabricación de EAD. Hablando más broaEl MEMTS podría ser una plataforma útil para el estudio de otros dispositivos que utilizan un acoplamiento termoeléctrico. Por ejemplo, podría utilizarse para observar los materiales utilizados en los enfriadores termoeléctricos, que convierten una tensión aplicada a una diferencia de temperatura a través del efecto Seebeck.
Aunque los experimentos realizados usando el proceso descrito aquí todavía tienen que demostrar que la deformación asistida eléctricamente se produce en ausencia de calentamiento Joule significativo, se necesitan experimentos adicionales. El proceso descrito aquí utilizó un pequeño conjunto de condiciones experimentales y se centró en una región localizada. Se necesita un conjunto más amplio de experimentos utilizando múltiples materiales, densidades de corriente y escalas de tiempo para verificar de manera más concluyente la existencia o ausencia de efectos puramente eléctricos en EAD. Una limitación técnica del enfoque actual de los MEMTS es la falta de capacidad para cuantificar la fuerza que actúa sobre un espécimen durante los experimentos in situ . La medida de fuerza es esencialPara obtener datos de tensión-deformación ( por ejemplo, para identificar cuantitativamente cuándo la muestra ha alcanzado el estrés de flujo) y, cuando se combina con observaciones in situ , proporciona directamente relaciones de estructura-propiedad. Hacia esta oportunidad única de investigación, actualmente estamos trabajando en la modificación de los marcos de Si para incorporar sensores de fuerza integrados.
Disclosures
Los autores declaran que no tienen intereses financieros en competencia.
Acknowledgments
Este trabajo fue apoyado por la beca postdoctoral ASEE-NRL y la Oficina de Investigación Naval a través del Programa de Investigación Básica del Laboratorio de Investigación Naval de los Estados Unidos. Los autores agradecen a C. Kindle en NRL por su apoyo técnico.
Materials
Name | Company | Catalog Number | Comments |
Silicon wafers | Any high-quality polished wafers of the correct thickness will work | ||
Photoresist | Dow | SR220-7 | |
Photoresist developer | Shipley | MF 24A | |
Photoresist developer | Rohm and Haas | MF 319 | |
Temporary wafer adhesive | Crystalbond 509 | Available from a variety of sources | |
Iductively Coupled Plasma Reactive Ion Etching (CP-RIE) system | Oxford | Plasmalab system 100 ICP RIE | |
Profilometer | Veeco | Dektak 150 | |
Plasma-Enhanced Chemical Vapor Deposition (PECVD) system | Oxford | Plasmalab system 100 PECVD | |
Thin specimen sheet | Surepure Chemetals | 3702, 3703, 3704 or 2236 | 13 µm and 25 µm-thick copper, 99.99% 4N Pure |
Photoresist | Shipley | 1818 | |
355 nm, 10 W, solid-state, frequency tripled Nd:YVO4 pulsed laser | JDSU | Q301-HD | |
Liquid ferric chloride | Sigma-Aldrich | 157740 | |
Conductive silver epoxy | Chemtronics | CW2400 | |
Silver wires | Any highly conductive metallic wires will work (<100 µm in diameter) | ||
Focused Ion Beam (FIB) | FEI | Nova 600 | |
Single tilt straining TEM holder | Gatan | 654 | |
Displacement controller | Gatan | 902 Accutroller | May be sold with the TEM holder |
CO2 laser cutter | Universal Laser Systems | VLS 3.50 | Use 50% power and 15% speed |
Electrical insulation sheet | 0.5 mm-thick Hard Fiber Electrical Grade Sheet (Fishpaper) | Available from a variety of sources | |
Transmission Electron Microscope (TEM) | FEI | Tecnai G2 | |
External power supply | Keithley | 2400 SourceMeter |
References
- Ross, C. D., Kronenberger, T. J., Roth, J. T. Effect of dc on the formability of Ti-6Al-4V. J Eng Mater-T ASME. 131 (3), 031004 (2009).
- Siopis, M. S., Kinsey, B. L. Experimental investigation of grain and specimen size effects during electrical-assisted forming. J Manuf Sci Eng-T ASME. 132 (2), 021004 (2010).
- Green, C. R., McNeal, T. A., Roth, J. T. Springback Elimination for Al-6111 Alloys Using Electrically Assisted Manufacturing (EAM). 37th Annual North American Manufacturing Research Conference. 37, Greenville, SC. 403-410 (2009).
- Okazaki, K., Kagawa, M., Conrad, H. A study of the electroplastic effect in metals. Scr Mater. 12 (11), 1063-1068 (1978).
- Sprecher, A. F., Mannan, S. L., Conrad, H. Overview no. 49. On the mechanisms for the electroplastic effect in metals. Acta Metall. 34 (7), 1145-1162 (1986).
- Perkins, T. A., Kronenberger, T. J., Roth, J. T. Metallic forging using electrical flow as an alternative to warm/hot working. J Manuf Sci Eng-T ASME. 129 (1), 84-94 (2007).
- Andrawes, J. S., Kronenberger, T. J., Perkins, T. A., Roth, J. T., Warley, R. L. Effects of DC current on the mechanical behavior of AlMg1SiCu. Mater Manuf Process. 22 (1), 91-101 (2007).
- Dzialo, C. M., Siopis, M. S., Kinsey, B. L., Weinmann, K. J. Effect of current density and zinc content during electrical-assisted forming of copper alloys. CIRP Ann Manuf Techn. 59 (1), 299-302 (2010).
- Fan, R., Magargee, J., Hu, P., Cao, J. Influence of grain size and grain boundaries on the thermal and mechanical behavior of 70/30 brass under electrically-assisted deformation. Mater Sci Eng A. 574, 218-225 (2013).
- Magargee, J., Morestin, F., Cao, J. Characterization of Flow Stress for Commercially Pure Titanium Subjected to Electrically Assisted Deformation. J Eng Mater Technol. 135 (4), 041003 (2013).
- Kinsey, B., Cullen, G., Jordan, A., Mates, S. Investigation of electroplastic effect at high deformation rates for 304SS and Ti-6Al-4V. CIRP Ann - Manuf Technol. 62 (1), 279-282 (2013).
- Williams, D. B., Carter, C. B. Transmission electron microscopy. , 2nd edn, Springer. (2008).
- Kang, W., Beniam, I., Qidwai, S. M. In situ electron microscopy studies of electromechanical behavior in metals at the nanoscale using a novel microdevice-based system. Rev Sci Instrum. 87 (9), (2016).
- Kim, M. J., et al. Electric current-induced annealing during uniaxial tension of aluminum alloy. Scr Mater. 75, 58-61 (2014).
- Knowles, M. R. H., Rutterford, G., Karnakis, D., Ferguson, A. Micro-machining of metals, ceramics and polymers using nanosecond lasers. Int J Adv Manuf Tech. 33 (1-2), 95-102 (2007).
- Kang, W., Saif, M. T. A. A novel SiC MEMS apparatus for in situ uniaxial testing of micro/nanomaterials at high temperature. J Micromech Microeng. 21 (10), (2011).
- Callister, W. D. Materials Science and Engineering: An Introduction. , 7th edn, John Wiley & Sons, Inc. (2007).
- Kang, W., Saif, M. T. A. A Novel Method for In Situ Uniaxial Tests at the Micro/Nano Scale-Part I: Theory. J Microelectromech Syst. 19 (6), 1309-1321 (2010).
- Kang, W., Han, J. H., Saif, M. T. A. A Novel Method for In Situ Uniaxial Tests at the Micro/Nanoscale-Part II: Experiment. J Microelectromech Syst. 19 (6), 1322-1330 (2010).
- Kang, W. M., Saif, M. T. A. In Situ Study of Size and Temperature Dependent Brittle-to-Ductile Transition in Single Crystal Silicon. Adv Func Mater. 23 (6), 713-719 (2013).
- Sim, G. D., Vlassak, J. J. High-temperature tensile behavior of freestanding Au thin films. Scr Mater. 75, 34-37 (2014).
- Haque, M. A., Saif, M. T. A. Deformation mechanisms in free-standing nanoscale thin films: A quantitative in situ transmission electron microscope study. Proc Natl Acad Sci U S A. 101 (17), 6335-6340 (2004).
- Zhu, Y., Espinosa, H. D. An electromechanical material testing system for in situ electron microscopy and applications. Proc Natl Acad Sci U S A. 102 (41), 14503-14508 (2005).
- Hosseinian, E., Pierron, O. N. Quantitative in situ TEM tensile fatigue testing on nanocrystalline metallic ultrathin films. Nanoscale. 5 (24), 12532-12541 (2013).
- Kang, W., Rajagopalan, J., Saif, M. T. A. In Situ Uniaxial Mechanical Testing of Small Scale Materials-A Review. Nanosci Nanotechnol Lett. 2 (4), 282-287 (2010).
- Kang, W., Merrill, M., Wheeler, J. M. In Situ Thermomechanical Testing Methods for Micro/Nano-Scale Materials. Nanoscale. , (2016).
- Thompson, K., Gorman, B., Larson, D., Bv Leer,, Hong, L. Minimization of Ga Induced FIB Damage Using Low Energy Clean-up. Microsc Microanal. 12 (S02), 1736-1737 (2006).
- Mayer, J., Giannuzzi, L. A., Kamino, T., Michael, J. TEM sample preparation and FIB-induced damage. MRS Bulletin. 32 (5), 400-407 (2007).